


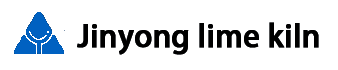
Lime kiln, as an indispensable equipment in the industrial field, is mainly used for the calcination process of limestone, thereby producing lime products widely used in various industries such as construction, metallurgy, and environmental protection.
1、 The basic composition of lime kiln
The lime kiln mainly consists of the following parts: kiln body, cooling equipment, hot air furnace, rotary support device, hopper and flue system, etc. Among them, the kiln body is the main part of the lime kiln, used to load limestone and calcine it; Cooling equipment is used to cool the lime after calcination is completed; The hot blast stove provides the heat energy required for combustion, ensuring that limestone undergoes decomposition reactions under high temperature conditions; The rotary support device is used to ensure the stability of the kiln body during the rotation process; The hopper is used to feed limestone into the kiln; The flue system is used to discharge the exhaust gas generated by combustion.
2、 The working principle of lime kiln
The working principle of a lime kiln mainly includes three stages: heating stage, calcination stage, and cooling stage. Below, a detailed introduction will be provided for each stage.
Heating stage
During the heating stage, limestone blocks are fed into the kiln through a hopper. At this point, the hot air stove starts working, sending coal gas and hot air into the kiln, creating a high-temperature and high-pressure reaction environment. During this process, the thermal energy generated by burning fuels such as coal, natural gas, or oil is directly or indirectly transferred to limestone through flames, allowing it to be preheated under high temperature conditions. The preheating process helps to increase the temperature inside the limestone, preparing it for the subsequent calcination stage.
Calcination stage
When the limestone reaches a certain preheating temperature, it enters the calcination stage. At this stage, limestone undergoes calcination reaction under high temperature conditions. When limestone is subjected to high-temperature thermal energy, its calcium carbonate (CaCO3) decomposes into calcium oxide (CaO) and carbon dioxide (CO2). This decomposition process is an endothermic reaction that requires continuous provision of heat energy to maintain a high-temperature environment. Meanwhile, the generated carbon dioxide is emitted into the atmosphere through the flue system, while calcium oxide is collected and used as a raw material for lime production.
It is worth noting that the temperature and time during the calcination stage have a significant impact on the quality of lime. Excessive temperature or time may lead to the sintering and agglomeration of lime, reducing its activity; If the temperature is too low or the time is too short, it may lead to incomplete decomposition of lime, affecting its quality and performance. Therefore, precise temperature and time control is required during the calcination stage to ensure that limestone can be fully decomposed and converted into high-quality calcium oxide.
Cooling stage
After calcination, limestone and cooling gas enter the cooling zone together for cooling. The main purpose of this process is to prevent premature solidification of lime and affect subsequent processing and use. The cooling process can be achieved through natural wind cooling or forced cooling through equipment such as fans. During the cooling process, the temperature of limestone gradually decreases and ultimately transforms into a solid lime product.
The cooling stage also has a significant impact on the quality of lime. If the cooling rate is too fast or the temperature is too low, it may cause cracks or powdering on the surface of the lime; If the cooling rate is too slow or the temperature is too high, it may lead to stress concentration or sintering inside the lime. Therefore, precise temperature and time control is also necessary during the cooling stage to ensure that lime can be uniformly cooled and converted into high-quality products.
3、 Technical characteristics of a new type of lime kiln
With the continuous development of technology, the new lime kiln adopts advanced production processes and technologies, which have the following significant technical characteristics:
Efficient energy consumption: The new lime kiln adopts advanced energy-saving technology, which can reduce energy consumption and improve energy utilization efficiency. By optimizing combustion systems and heat recovery systems, efficient combustion and effective utilization of thermal energy have been achieved.
High degree of automation: The new lime kiln is equipped with advanced automation control systems and monitoring equipment, which can achieve real-time monitoring and automatic adjustment of parameters such as temperature, pressure, flow rate, etc. This not only improves production efficiency but also reduces the risk of human operation.
Good environmental performance: The new lime kiln adopts low emission technology and flue gas treatment system during the combustion process, effectively reducing exhaust gas emissions and environmental pollution. At the same time, advanced dust removal equipment and noise control measures have been adopted, further improving environmental performance.
As an important industrial equipment, the working principle of lime kiln involves multiple stages such as heating, calcination, and cooling. By precisely controlling temperature and time, as well as adopting advanced production processes and technological means, high-quality lime products can be produced and widely applied in various fields. With the continuous progress of technology, new lime kilns have also made significant contributions to the development of the industrial field in terms of high energy consumption, automation level, and environmental performance.