


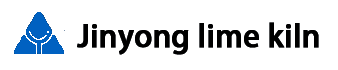
As a key equipment for producing lime, the operating efficiency of lime kilns is directly related to product quality. However, in the actual production process, the problem of high ash discharge temperature from lime kilns often occurs, which not only reduces production efficiency, but also wastes energy and even affects the quality of the final product. Therefore, a reasonable analysis and handling of this issue is crucial.
1、 Analysis of the Reasons for High Ash Discharge Temperature in Lime Kilns
1. Fuel combustion issues
The heating of lime kilns mainly relies on fuels such as coal and natural gas. If there is too much fuel supply, the combustion process may overheat, leading to an increase in the temperature of the ash. In addition, insufficient fuel combustion is also a common problem. During the combustion process, if the fuel is not completely burned, a large amount of combustible gases and unburned carbon will remain. These substances continue to burn at high temperatures, further pushing up the ash discharge temperature.
2. Insufficient oxygen supply
Oxygen is an essential substance for combustion. If the oxygen supply in the kiln is insufficient, the combustion reaction will become incomplete, generating too much heat and accumulating in the kiln, leading to an increase in the ash discharge temperature.
3. Lime kiln structure and design issues
The structure, size, and design of the lime kiln may have issues, resulting in uneven distribution of heat. For example, there may be localized high-temperature areas inside the kiln, where heat is concentrated, resulting in a significant increase in ash temperature. In addition, poor insulation effect and large heat loss of the kiln body can indirectly lead to an increase in ash discharge temperature.
4. Changes in raw material properties
The decomposition rate and reaction activity of different types of limestone vary at different temperatures. If the properties of the raw materials change, such as a decrease in CaCO3 content or an increase in impurities in limestone, it may lead to insufficient heat absorption during the decomposition process or uneven reaction rate, resulting in an increase in ash discharge temperature.
5. Automatic control system malfunction
The automatic control system plays a crucial role in the operation of the lime kiln. If there is a malfunction or instability in the system, it may result in the inability to effectively control the temperature inside the kiln, leading to the problem of high ash discharge temperature.
6. Other factors
In addition to the above factors, there are also some other factors that may cause high ash discharge temperature in the lime kiln, such as nodulation inside the kiln, high coke ratio, poor cooling effect, equipment failure, etc.
2、 Treatment methods for high ash discharge temperature in lime kilns
We can start from the following aspects and adopt corresponding treatment methods to address the high ash discharge temperature of lime kilns.
1. Reasonably control fuel supply
Firstly, the supply of fuel should be reasonably controlled to ensure that there is not too much supply of fuel. This can be achieved by adjusting the flow rate of gas supply or using more efficient burners. At the same time, strengthen the monitoring of fuel combustion to ensure that the combustion process is complete and stable. The problem of insufficient fuel combustion can be solved by optimizing fuel formulations, improving combustion efficiency, and other methods.
2. Ensure sufficient oxygen supply inside the kiln
Oxygen is a necessary condition for combustion, so it should be ensured that there is sufficient oxygen supply in the kiln. This can be achieved by monitoring oxygen concentration and adjusting the oxygen supply system. During the combustion process, an appropriate amount of air should be maintained to allow the fuel to burn fully. The problem of insufficient oxygen supply can be solved by increasing ventilation and adjusting fan speed.
3. Improve the structure and design of the kiln
Corresponding improvement measures can be taken to address the problems in the structure and design of the kiln. For example, optimizing the structure of the kiln and adding a heat sharing device to improve the uniformity of heat distribution. At the same time, strengthen the insulation effect of the kiln body and reduce heat loss. For local high temperature areas, solutions can be achieved by adjusting the burner position and adding heat dissipation devices.
4. Regularly check the properties of raw materials
The change in raw material properties is one of the important factors affecting the temperature of lime kiln ash discharge. Therefore, the properties of limestone should be regularly checked to ensure stable quality of raw materials. If there is a change in quality, the procurement source or processing method of limestone should be adjusted in a timely manner. At the same time, strengthen the pre-treatment of raw materials, such as crushing, screening, etc., to improve the uniformity and reactivity of the raw materials.
5. Maintenance and inspection of automatic control system
The automatic control system plays a crucial role in the operation of the lime kiln. Therefore, the automatic control system should be regularly maintained and inspected to ensure its stable operation. For existing faults or unstable situations, the system should be repaired or upgraded in a timely manner. At the same time, strengthen the training and management of operators to improve their ability to operate and respond to faults in automatic control systems.
6. Ventilation and cooling
Ventilation is one of the effective means to regulate the temperature inside the lime kiln. The ventilation effect inside the kiln can be strengthened by increasing the ventilation volume, adjusting the fan speed, and other methods. In addition, during the cooling stage after ash discharge, it should be ensured that the cooling effect is good. Cooling efficiency can be improved by increasing the number of cooling fans and adjusting the flow rate of cooling water. For issues with poor cooling effectiveness, it is possible to consider adding cooling devices or optimizing cooling processes.
7. Dealing with nodulation and coke ratio issues inside the kiln
The formation of nodules and excessive coke ratio inside the kiln are also one of the reasons for the increase in ash discharge temperature. The problem of nodules inside the kiln can be solved by regularly cleaning the nodules and optimizing the combustion process. For the problem of excessive coke ratio, the supply of coke can be appropriately reduced or the particle size distribution of coke can be adjusted to improve combustion efficiency.