


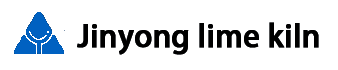
In the process of lime production, the phenomenon of environmental protection lime kiln firing is a key concern. Setting fire may not only affect the quality of lime, but may also cause damage to kiln equipment and even endanger production safety. Therefore, it is crucial to understand the causes and preventive measures of fire in environmentally friendly lime kilns.
1、 Phenomenon and causes of downfire
The ignition of environmentally friendly lime kilns usually refers to the abnormal combustion phenomenon that occurs during the calcination process, manifested as flame downward movement or local high temperature inside the kiln. There are various reasons for catching fire, mainly including the following aspects:
Raw material issue:
Improper particle size of limestone is an important cause of fire. When the size of limestone particles is too large, the calcination speed slows down, which may cause local temperatures inside the kiln to be too high; When the particle size is too small, it is easy to cause poor air permeability in the kiln, which can also cause ignition.
Excessive content of soil or other impurities in the raw materials can also affect the stability of the calcination process and increase the risk of ignition.
Improper operation:
Excessive or rapid ash discharge can cause the calcination belt to move down too quickly, leading to ignition. Operators need to be cautious when controlling the speed and quantity of ash discharge to avoid temperature fluctuations caused by this.
Equipment malfunction or design defect:
If the lump blocks the lower ash outlet or the structure design inside the kiln is not reasonable, it may lead to poor airflow in the kiln, local high temperature, and thus cause fire.
Air and fuel supply issues:
Unreasonable air supply is another important cause of fire. Excessive or insufficient air flow can affect the combustion status of fuel, thereby affecting the distribution of temperature inside the kiln. The choice of fuel and combustion rate also have a significant impact on the temperature inside the kiln. If the fuel combustion speed is too fast, it may cause a sudden increase in local temperature and trigger a fire.
2、 Prevention and Response Measures for Downfire
For the above reasons, the following prevention and response measures can be taken:
Strictly control the quality of raw materials:
Choose limestone with appropriate particle size for calcination, avoiding excessive or insufficient particle size.
Reduce the impurity content in raw materials, especially substances such as soil that can lead to poor air permeability in the kiln.
Standardized operation:
Train operators to master the control skills of ash discharge speed and quantity proficiently, ensuring the stability of the calcination belt.
Regularly clean and maintain the kiln to prevent obstacles such as lumps from affecting the airflow and temperature distribution.
Optimize device design:
Improve the structural design of the kiln to ensure smooth airflow and avoid local high temperatures. Select efficient and stable combustion equipment and air supply system to ensure sufficient combustion of fuel and uniform temperature distribution.
Strengthen monitoring and emergency response:
Install temperature sensors and monitoring equipment at critical locations inside the kiln to monitor temperature changes in real-time.
Develop emergency plans and take immediate measures to deal with any abnormal situations such as fires, in order to prevent the situation from escalating.
The phenomenon of fire in environmentally friendly lime kilns is a complex problem that requires prevention and control from multiple aspects. Only by strictly controlling the quality of raw materials, standardizing operations, optimizing equipment design, and strengthening monitoring and emergency response can we ensure the stability and safety of lime production.