


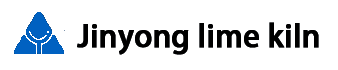
With the increasing awareness of environmental protection and the continuous increase in energy costs, reducing coal consumption in industrial furnaces and kilns has become the key for enterprises to reduce costs and improve competitiveness. As the main equipment for lime production, the reduction of coal consumption in lime kilns is of great significance for the entire lime industry and even the entire industrial sector. In recent years, with the continuous innovation and progress of technology, new lime kilns have achieved significant results in reducing coal consumption.
1、 Design of New Lime Kiln to Reduce Coal Consumption
Optimize the furnace structure
The new lime kiln fully considers the demand for energy conservation and consumption reduction in its design, optimizing the furnace structure to improve thermal efficiency and reduce coal consumption. For example, adopting a double-layer furnace wall structure to increase the thickness of the insulation layer and reduce heat loss; Reasonably design the shape and size of the furnace to ensure more complete fuel combustion and improve combustion efficiency.
Improving the combustion system
The new lime kiln adopts advanced combustion technologies such as pulse combustion and oxygen rich combustion, making the fuel more sufficient and stable during the combustion process. At the same time, by optimizing the structure and layout of the burner, the mixture of fuel and air is more uniform, improving combustion efficiency. In addition, the new lime kiln is also equipped with an automatic control system, which can adjust combustion parameters in real-time according to production needs, ensuring that the combustion process is always in the best state.
Enhanced heat recovery
The new lime kiln has strengthened heat recovery measures in its design, such as setting up flue gas recovery systems, waste heat recovery devices, etc., to recover and utilize the heat in the flue gas and reduce energy loss. Meanwhile, by optimizing the structure and layout of the heat recovery system, the efficiency of heat recovery can be improved and coal consumption can be further reduced.
2、 Technological optimization reduces coal consumption
Raw material pretreatment
The pretreatment of raw materials plays an important role in reducing coal consumption. By screening, crushing, drying and other pre-treatments of raw materials, the uniformity and combustion performance of the materials can be improved, making the fuel more complete and stable during the combustion process. Meanwhile, pretreatment can also reduce the moisture content of raw materials, reduce heat loss, and lower coal consumption.
Fuel selection and substitution
Reasonably selecting fuels and exploring alternative energy sources are effective ways to reduce coal consumption. The new lime kiln prioritizes high-quality fuels with low sulfur and low ash content in fuel selection to reduce pollutant emissions during combustion. At the same time, actively exploring alternative energy sources such as biomass and solar energy to reduce dependence on coal and further reduce coal consumption.
Optimization of combustion process
The optimization of the combustion process is a key link in reducing coal consumption. The new lime kiln adopts measures such as adjusting combustion parameters, optimizing burner structure and layout, etc., to make the fuel more sufficient and stable during the combustion process. At the same time, strengthen the monitoring and regulation of the combustion process, ensure that the combustion process is always in the best state, improve combustion efficiency, and reduce coal consumption.
3、 Operational management reduces coal consumption
Strengthen employee training
Strengthening employee training is the foundation for reducing coal consumption. Through training, employees can master the operating procedures and precautions of the new lime kiln, improve their operating skills and safety awareness. Meanwhile, training can also help employees understand the importance of energy conservation and consumption reduction, enhance their awareness of energy conservation, and thus reduce coal consumption.
Implement refined management
Implementing refined management is an effective means of reducing coal consumption. By real-time monitoring and data analysis of the operating status and combustion parameters of the lime kiln, problems can be identified and resolved in a timely manner to ensure the stable operation of the lime kiln. At the same time, strengthen equipment maintenance and upkeep, extend the service life of equipment, and reduce the increase in energy consumption caused by equipment failures.
Develop energy-saving and consumption reduction measures
Developing energy-saving and consumption reduction measures is the key to reducing coal consumption. Based on the actual situation and production needs of the lime kiln, targeted energy-saving and consumption reduction measures are formulated, such as optimizing the raw material ratio, adjusting combustion parameters, and strengthening heat recovery. At the same time, strengthen the implementation and supervision of energy-saving and consumption reduction measures to ensure their effective implementation.
The new lime kiln has effectively reduced coal consumption through measures such as optimized design, technical optimization, and operational management. These measures not only improve the thermal and combustion efficiency of lime kilns, but also reduce production costs and pollutant emissions, achieving a win-win situation of economic and environmental benefits. In the future, with the continuous innovation and progress of technology, new lime kilns will achieve more significant results in reducing coal consumption.