


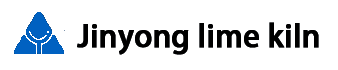
Lime kilns, as the main equipment for producing lime, have a wide range of applications in metallurgy, chemical industry, building materials, and other fields. However, lime kilns consume a significant amount of energy during operation, which not only increases production costs but also puts pressure on the environment. Therefore, reducing the energy consumption of lime kilns and improving their energy efficiency level is of great significance for promoting the sustainable development of enterprises.
1、 Analysis of Energy Consumption Status of Lime Kiln
The energy consumption of lime kilns mainly includes two parts: fuel consumption and electricity consumption. Fuel consumption is mainly used to provide the heat required for limestone decomposition, while electricity consumption is mainly used for the operation of lime kilns and auxiliary equipment. At present, the energy consumption of lime kilns is generally high, mainly due to the following reasons: The design of the lime kiln is unreasonable and the thermal efficiency is low. Some lime kilns did not fully consider factors such as raw material characteristics and operating conditions in their design, resulting in low thermal efficiency and high energy consumption.
The fuel quality is unstable and the combustion efficiency is low. The instability of fuel quality can affect combustion efficiency, thereby increasing energy consumption.
Improper operational management and serious energy waste. Some lime kilns have problems such as non-standard operation and inadequate management during the operation process, resulting in serious energy waste.
2、 The main factors affecting energy consumption in lime kilns
The structure and design of a lime kiln. The structure and design of a lime kiln directly affect its thermal efficiency and energy consumption. Reasonable structural design and optimized operating parameters can improve thermal efficiency and reduce energy consumption.
Raw material characteristics. The chemical composition, particle size, moisture and other characteristics of raw materials have a significant impact on the energy consumption of lime kilns. For example, excessive moisture in raw materials can increase energy consumption.
Fuel quality. The stability of fuel quality and combustion efficiency have a direct impact on the energy consumption of lime kilns. High quality fuel can improve combustion efficiency and reduce energy consumption.
Operational management level. The level of operational management directly affects the operational efficiency and energy consumption of lime kilns. Standardized operational management and scientific maintenance can reduce energy consumption.
3、 Strategies and practices for reducing energy consumption in lime kilns
Optimize the design and structure of lime kilns
(1) Adopting an efficient and energy-saving lime kiln. Efficient and energy-saving lime kilns adopt advanced combustion and heat exchange technologies, which can improve thermal efficiency and reduce energy consumption.
(2) Optimize the kiln structure. By optimizing the kiln structure, such as adding preheating sections and improving the combustion chamber structure, the thermal efficiency of the lime kiln can be improved. (3) Optimize kiln body materials. Choosing materials with good thermal conductivity as kiln materials can improve heat transfer efficiency and reduce energy consumption.
Improving fuel quality and combustion efficiency
(1) Choose high-quality fuel. Choosing fuels with high calorific value and stable combustion can improve combustion efficiency and reduce energy consumption.
(2) Adopting advanced combustion technology. The use of premixed combustion technology, pulse combustion technology, etc. can improve combustion efficiency and reduce energy consumption.
(3) Optimize the combustion control system. By optimizing the combustion control system, precise control and automatic adjustment of fuel can be achieved, which can improve combustion efficiency and reduce energy consumption.
Strengthen operation management and maintenance
(1) Standardize operating procedures. Develop detailed operating procedures and procedures to ensure that operators operate in accordance with regulations and reduce energy waste.
(2) Strengthen maintenance and upkeep. Regularly maintain the lime kiln, check the operation status of the equipment, promptly identify and solve problems, and ensure the normal operation of the equipment. (3) Strengthen energy management. Establish an energy management system, monitor and analyze energy consumption, and take timely measures to reduce energy consumption.
Utilizing waste heat recovery technology
(1) Adopting flue gas recirculation technology. Recycling and reusing the heat in flue gas can reduce energy consumption.
(2) Adopting heat pipe technology. Using heat pipe technology to transfer heat from high-temperature flue gas to other media, achieving heat recovery and utilization.
(3) Utilizing pyrolysis oil recovery technology. The pyrolysis oil generated by the lime kiln can be recycled and reused as fuel, reducing energy consumption.
Reducing the energy consumption of lime kilns is the key to improving their energy efficiency, reducing production costs, and promoting sustainable development. By optimizing the design and structure of the lime kiln, improving fuel quality and combustion efficiency, strengthening operational management and maintenance, and utilizing waste heat recovery technology, the energy consumption of the lime kiln can be effectively reduced. In the future, with the continuous progress and innovation of technology, it is believed that more efficient and energy-saving technologies will be applied to the production of lime kilns, injecting new impetus into the sustainable development of enterprises.