


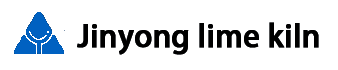
The quality of refractory materials is crucial in the construction of lime kiln shaft kilns. It not only relates to the service life and production efficiency of the kiln, but also directly affects the quality of the product and the economic benefits of the enterprise. The following are the quality requirements for refractory materials in the construction of lime kiln shaft kiln.
1、 High temperature resistance performance
During the operation of the lime kiln shaft kiln, the internal temperature is extremely high, usually reaching thousands of degrees Celsius. Therefore, refractory materials must have excellent high-temperature resistance and be able to maintain stable physical and chemical properties in high-temperature environments.
High refractoriness
The refractoriness of refractory materials refers to their performance of not softening or melting under high temperature. For lime kiln shaft kiln, the refractoriness of refractory materials should be higher than the maximum working temperature inside the kiln to ensure that there will be no softening, deformation or even melting under long-term high-temperature operation.
Good thermal stability
Thermal stability refers to the ability of refractory materials to resist cracking and peeling during rapid temperature changes. The temperature of the lime kiln shaft kiln often changes during the start-up, shutdown, and production process. Therefore, refractory materials must have good thermal stability and be able to withstand frequent temperature fluctuations without cracking, peeling, or other phenomena.
2、 Chemical resistance performance
The materials inside the lime kiln shaft kiln undergo a series of complex chemical reactions at high temperatures, producing various corrosive gases and slag. Refractory materials must have good chemical resistance to resist the erosion of these corrosive substances. Resistance to alkaline erosion
The materials inside the lime kiln shaft kiln are mainly alkaline substances such as limestone, which will produce alkaline slag and gas at high temperatures. Refractory materials should have good resistance to alkaline erosion and be able to maintain stable performance in alkaline environments. For example, high alumina refractory materials and magnesium refractory materials exhibit good resistance to alkaline corrosion.
Acid resistant erosion
Although the environment inside the lime kiln shaft kiln is mainly alkaline, in some cases, it may also be corroded by acidic substances. For example, impurities in fuel may produce acidic gases after combustion. Therefore, refractory materials should also have a certain resistance to acid erosion to improve their adaptability in complex environments.
3、 Mechanical strength
During the operation of the lime kiln shaft kiln, the refractory materials are subjected to mechanical effects such as material impact, wear, and expansion and contraction of the kiln body. Therefore, refractory materials must have sufficient mechanical strength to ensure that they will not be damaged under various mechanical stresses.
High compressive strength
The compressive strength refers to the pressure that refractory materials can withstand per unit area. For lime kiln shaft kiln, the compressive strength of refractory materials should be high enough to withstand the pressure of materials inside the kiln and the weight of the kiln body. Generally speaking, high alumina refractory materials and silicon carbide refractory materials have higher compressive strength.
High flexural strength
Flexural strength refers to the ability of refractory materials to resist damage under bending stress. In a lime kiln shaft kiln, refractory materials may experience bending stress due to factors such as expansion and contraction of the kiln body and uneven distribution of materials. Therefore, the flexural strength of refractory materials should also be high to ensure that they will not fracture in complex stress environments.
Good wear resistance
The materials inside the lime kiln shaft kiln will cause wear and tear on the refractory materials during their movement. Especially in the lower part of the kiln and the discharge port, the wear is more severe. Therefore, refractory materials should have good wear resistance to extend their service life. For example, silicon carbide refractory materials and corundum refractory materials exhibit excellent wear resistance.
4、 Thermal insulation performance
Good insulation performance can reduce the heat loss of the kiln body, improve energy utilization efficiency, and reduce production costs. At the same time, it can also protect the equipment and buildings around the kiln body, improving production safety.
Low thermal conductivity
Thermal conductivity is an important indicator for measuring the thermal insulation performance of refractory materials. The lower the thermal conductivity, the better the insulation performance of refractory materials. For lime kiln shaft kiln, refractory materials with low thermal conductivity should be selected to reduce the heat loss of the kiln body. For example, lightweight refractory materials and ceramic fiber materials have low thermal conductivity and good insulation performance.
Low bulk density
Volume density refers to the mass per unit volume of refractory materials. Refractory materials with low bulk density usually have good thermal insulation performance. When selecting refractory materials, it is advisable to choose materials with lower bulk density to improve the insulation effect of the kiln body.
5、 Construction performance
The construction performance of refractory materials directly affects the quality and progress of kiln construction. Therefore, when selecting refractory materials, their construction performance should also be considered. Good plasticity
Plasticity refers to the ability of refractory materials to deform at a certain temperature and pressure. Refractory materials with good plasticity are easy to construct and can better adapt to changes in the shape and size of kilns. For example, plastic and ramming materials can be filled into various parts of the kiln through ramming, squeezing, and other methods during the construction process to ensure construction quality.
Strong adhesion
Adhesive properties refer to the bonding ability between refractory materials and the kiln body or other refractory materials. Refractory materials with strong adhesion can ensure the integrity and sealing of the kiln, preventing gas and material leakage. For example, refractory mud and refractory adhesive can have a good bonding effect during the construction process.
Dry shrinkage is small
Refractory materials need to be dried after construction to remove moisture. If the drying shrinkage is too large, it may cause cracks and peeling of refractory materials, affecting the service life of the kiln. Therefore, dry and reduced refractory materials should be selected to ensure construction quality.
The construction of lime kiln shaft kiln requires very strict quality requirements for refractory materials. When selecting refractory materials, factors such as high temperature resistance, chemical resistance, mechanical strength, thermal insulation performance, and construction performance should be comprehensively considered to select suitable refractory materials to ensure the stable operation and long-term use of the kiln.