


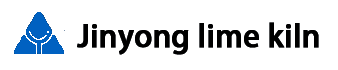
1、 Design features
Efficient production capacity: The environmentally friendly lime vertical kiln with a daily output of 300 tons adopts advanced production technology and structural design, which greatly improves its production efficiency. On the premise of ensuring product quality, the goal of high production capacity and low energy consumption has been achieved.
Environmental protection and energy conservation: The lime vertical kiln has fully considered environmental factors in the design process, adopting multiple environmental protection measures such as low nitrogen combustion technology, flue gas desulfurization and denitrification technology, and high-efficiency dust removal technology, effectively reducing the emission of pollutants. Meanwhile, by optimizing the combustion system and heat recovery system, efficient energy utilization has been achieved and energy consumption has been reduced.
Intelligent control: The lime vertical kiln is equipped with an advanced intelligent control system, which can monitor key parameters such as temperature, pressure, and gas composition in real-time inside the kiln, and automatically adjust the combustion status and emission parameters according to the actual situation. This not only improves the stability and safety of the production process, but also further reduces the possibility of human operational errors.
Modular design: In order to facilitate transportation and installation, the lime vertical kiln adopts a modular design. Standardized interfaces are used to connect various modules, making the installation process easier and faster. At the same time, modular design also makes equipment maintenance and upgrades more convenient.
2、 Working principle
The working principle of an environmentally friendly lime vertical kiln with a daily output of 300 tons is mainly based on the calcination process of limestone. In the kiln, limestone undergoes stages such as preheating, decomposition, and cooling before ultimately being converted into lime. The specific process is as follows:
Preheating stage: Limestone is added from the kiln top and first enters the preheating zone. Here, limestone exchanges heat with the high-temperature gas inside the kiln, gradually increasing the temperature.
Decomposition stage: The preheated limestone enters the decomposition zone. In this area, limestone undergoes decomposition reactions at high temperatures, producing calcium oxide (i.e. lime) and carbon dioxide.
Cooling stage: The decomposed lime enters the cooling zone. Here, lime exchanges heat with the cold air entering the kiln, reduces temperature, and is discharged outside the kiln. At the same time, cold air absorbs heat and becomes a high-temperature gas, which enters the preheating zone for recycling. Throughout the entire calcination process, the intelligent control system monitors and adjusts parameters such as temperature and pressure inside the kiln in real-time to ensure the stability of the production process and product quality. Meanwhile, by optimizing the combustion system and heat recovery system, efficient energy utilization and pollutant reduction can be achieved.
3、 Environmental advantages
Low emissions: The environmentally friendly lime vertical kiln with a daily output of 300 tons adopts advanced flue gas desulfurization and denitrification technology and efficient dust removal technology, which significantly reduces the emissions of pollutants such as sulfur dioxide, nitrogen oxides, and dust in the flue gas. In addition, optimizing the combustion system to reduce the generation of pollutants such as nitrogen oxides further enhances environmental performance.
Energy saving and consumption reduction: The lime vertical kiln achieves efficient energy utilization by optimizing the combustion system and heat recovery system. The heat generated by the decomposition of limestone at high temperatures is fully recovered and utilized to preheat the limestone and air entering the kiln, thereby reducing energy consumption. At the same time, the intelligent control system monitors and adjusts the combustion status in real time to ensure the efficient and stable combustion process. Comprehensive utilization of resources: The by-products such as exhaust gas and waste residue generated by lime vertical kilns can be processed to achieve resource utilization. For example, carbon dioxide in exhaust gas can be used to prepare carbonated beverages or as a chemical raw material; Waste residue can be used for the production of building materials or as a soil amendment. This not only reduces production costs but also achieves the recycling of resources.
4、 Application prospects
With the continuous tightening of environmental policies and the intensification of market competition, more and more enterprises are paying attention to green production and sustainable development. The daily output of 300 tons of environmentally friendly lime vertical kiln has broad application prospects in the field of lime production due to its high efficiency, environmental protection, energy conservation, and intelligent control. In the future, with the continuous progress of technology and the continuous expansion of the market, the lime vertical kiln will be applied in more fields and promote the green transformation and upgrading of the entire industry.