


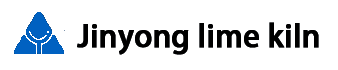
The traditional lime production process is often accompanied by high energy consumption and emissions, which not only exacerbates the energy shortage situation, but also causes serious pollution to the environment. In response to this challenge, efficient lime kilns have emerged.
The high-efficiency lime kiln has achieved the goals of energy conservation, emission reduction, capacity improvement, and cost reduction in the lime production process through a series of technological innovations and optimized designs. Firstly, the high-efficiency lime kiln adopts advanced kiln structure design, such as reasonable layout of preheating zone, calcination zone, and cooling zone, as well as optimized selection of insulation materials, effectively reducing heat loss and improving thermal efficiency. This design not only improves the production efficiency of lime, but also reduces energy consumption, thereby reducing production costs.
Secondly, the high-efficiency lime kiln has been improved in terms of combustion system. By adopting technologies such as high-efficiency burners and flue gas recirculation, the full combustion of fuel and effective utilization of heat have been achieved. Meanwhile, by precisely controlling the oxygen content and temperature during the combustion process, the combustion efficiency is further improved. This not only reduces fuel waste, but also lowers exhaust emissions and improves environmental performance.
In addition to the improvement of kiln structure and combustion system, the high-efficiency lime kiln has also introduced advanced automation control system. The system can monitor real-time parameters such as temperature, pressure, and oxygen content inside the kiln, and automatically adjust fuel supply, air volume, etc. according to the set values to ensure the stability and efficiency of the production process. This automation control not only improves production efficiency, but also reduces manual operation errors and enhances product quality.
In terms of raw material processing, the high-efficiency lime kiln has also been optimized. By pre-treatment and preheating of raw materials, the particle size is ensured to be uniform, and the kiln temperature is increased, thereby improving the production efficiency of lime. At the same time, for fuels such as coke, the combustion speed and efficiency are improved by controlling the particle size, further reducing production costs.
In addition, efficient lime kilns also pay attention to the treatment of waste gas and the recovery of resources. By installing dust collectors, desulfurization and denitrification devices and other waste gas treatment facilities, the exhaust gas emitted from the kiln is purified, reducing pollutant emissions. At the same time, the use of waste heat from exhaust gas for preheating and power generation resource recovery has achieved the recycling of energy.
The high-efficiency lime kiln has achieved the goals of energy conservation, emission reduction, capacity improvement, and cost reduction in the lime production process by optimizing the kiln structure, improving the combustion system, introducing automated control systems, optimizing raw material processing, and focusing on waste gas treatment and resource recovery. This not only creates greater economic and social benefits for enterprises, but also promotes the sustainable development of the lime industry. In the future, with the continuous advancement and innovation of technology, efficient lime kilns will usher in a broader development prospect.