


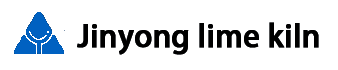
Against the backdrop of increasingly scarce energy resources and stricter environmental protection requirements, vertical lime kilns have become the focus of lime production due to their significant low unit energy consumption advantage. This advantage not only reduces production costs and enhances market competitiveness for enterprises, but also makes important contributions to sustainable development.
1、 Structural optimization and energy-saving principle of vertical kiln
The low unit energy consumption of lime kiln vertical kiln is primarily due to its carefully designed structure. The unique layout and structure inside the vertical kiln can achieve efficient utilization and transfer of heat.
The kiln body usually uses multiple layers of insulation materials, effectively reducing heat loss. At the same time, a reasonable ventilation system ensures sufficient supply of oxygen during the combustion process, improves the combustion efficiency of fuel, and thus reduces energy consumption.
For example, setting specific ventilation openings at the top and bottom of the kiln can create natural airflow circulation, evenly distribute heat, avoid local overheating or overcooling, and improve overall heat utilization efficiency.
2、 Advanced combustion technology
In order to further reduce energy consumption, the lime kiln vertical kiln adopts a series of advanced combustion technologies. Efficient burners can fully atomize fuel, increase the contact area with air, and achieve more complete combustion. In addition, the intelligent combustion control system can accurately adjust the fuel supply and combustion conditions based on real-time production parameters and raw material characteristics, avoiding energy waste.
Taking a vertical kiln fueled by natural gas as an example, by precisely controlling the ratio of air to natural gas during the combustion process, not only is the combustion temperature increased, but also the unburned components in the exhaust gas are reduced, resulting in a decrease in unit energy consumption.
3、 Selection and pretreatment of raw materials
The appropriate selection and pretreatment of raw materials also play a key role in reducing unit energy consumption. High quality limestone raw materials have high purity and uniform particle size distribution, which can decompose faster during the calcination process, reducing the required heat and time. At the same time, appropriate crushing and screening of raw materials to make them uniform in size is beneficial for uniform heating and reaction inside the kiln, improving energy utilization efficiency. For example, selecting high-grade limestone and crushing it into suitable particle size can significantly shorten calcination time and reduce energy consumption.
4、Waste heat recovery and utilization
During the operation of a vertical lime kiln, a large amount of waste heat is generated. Through an effective waste heat recovery system, these previously wasted thermal energy can be reused.
Waste heat can be used to preheat the air and raw materials entering the kiln, reducing fuel consumption. Or convert waste heat into electrical energy to provide power for other production processes.
For example, installing a heat exchanger transfers the heat from high-temperature exhaust gas to cold air and cold raw materials, achieving energy recycling and significantly reducing unit energy consumption.
5、 Intelligent monitoring and management
With the help of advanced sensors and monitoring equipment, the lime kiln vertical kiln has achieved real-time monitoring of the production process.
An intelligent management system can collect and analyze various data such as temperature, pressure, flow rate, etc., timely detect abnormal energy consumption situations, and automatically adjust operating parameters to maintain the optimal energy consumption level. For example, when the temperature in a certain area is detected to be too high, the system will automatically reduce the fuel supply in that area to avoid energy waste caused by overheating.
6、 The economic and environmental benefits brought by low energy consumption
The reduction of unit energy consumption has brought significant economic benefits to enterprises.
Reducing fuel usage directly lowers production costs. Meanwhile, lower energy consumption also means less equipment wear and maintenance costs, extending the lifespan of the equipment.
In terms of the environment, low energy consumption means less greenhouse gas emissions and pollutant production, which meets the requirements of today's society for green production.
Assuming a vertical kiln with an annual output of 100000 tons of lime, by reducing unit energy consumption, a significant amount of fuel costs can be saved each year, and corresponding carbon dioxide emissions can be reduced, establishing a good image for the sustainable development of the enterprise.
The vertical lime kiln has achieved a significant reduction in unit energy consumption due to its advantages in structure, combustion technology, raw material processing, waste heat recovery, and intelligent management. This not only brings dual economic and environmental benefits to lime production enterprises, but also points out the direction for the sustainable development of the entire industry. In the future, we have reason to believe that vertical lime kilns will continue to innovate and progress on the path of low energy consumption, making greater contributions to building a resource-saving and environmentally friendly society.