


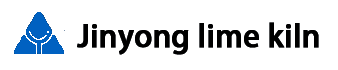
As an important equipment for producing lime, the operating efficiency and product quality of lime kilns have a crucial impact on many industries. The traditional lime kiln control system often has problems such as inconvenient operation, low accuracy, and high energy consumption, which seriously restrict the improvement of production efficiency. As a professional enterprise in the industry, Jinyong Kiln is committed to providing users with lime kiln automation upgrade and transformation services. Through advanced technology and comprehensive solutions, it helps enterprises achieve intelligent, efficient, and sustainable development of lime kiln production.
1、 Current situation and problem analysis of lime kiln automation control system
(1) Current situation
At present, many lime kilns still use outdated control systems, mainly relying on manual operation and simple instrument monitoring. The control accuracy of key parameters such as temperature, pressure, and gas flow rate in the production process is limited, making it difficult to achieve precise control. Meanwhile, the recording and analysis of production data mostly rely on manual labor, lacking systematicity and real-time capability.
(2) Existing issues
Poor operational stability
Traditional control systems are susceptible to external interference, such as voltage fluctuations, environmental temperature changes, etc., which can lead to unstable operating conditions of lime kilns and affect the consistency of product quality.
Serious energy waste
Due to the inability to precisely control the combustion process, excessive fuel consumption often occurs. For example, when the temperature inside the kiln is too high, the fuel supply cannot be adjusted in a timely manner, resulting in unnecessary waste of energy.
High maintenance costs
The frequent malfunctions and inaccurate control of equipment lead to accelerated wear and tear of components, requiring frequent maintenance and replacement, which increases the maintenance costs of the enterprise.
Low production efficiency
The limitations of manual operation result in delayed adjustments and optimizations during the production process, longer production cycles, and difficulty in increasing output.
2、 Overview of the Automation Upgrade and Renovation Plan for Jinyong Kiln
(1) Overall objective
By introducing advanced automation technology, precise control, real-time monitoring, and intelligent optimization of the lime kiln production process can be achieved, improving production efficiency, reducing energy consumption, enhancing product quality, while reducing manual intervention and labor intensity.
(2) Specific measures
Hardware upgrade
(1) By using high-precision sensors such as temperature sensors, pressure sensors, gas concentration sensors, etc., various parameters inside the kiln can be collected in real-time and accurately.
(2) Update the controller equipment and select high-performance PLC (Programmable Logic Controller) or DCS (Distributed Control System) to improve the accuracy and stability of control.
(3) Install advanced actuators such as regulating valves, frequency converters, etc. to achieve precise adjustment of fuel, air, and other flow rates.
Software system development
(1) Design a user-friendly human-machine interface, allowing operators to intuitively understand the operating status inside the kiln, facilitating parameter settings and operational control.
(2) Develop intelligent control algorithms to automatically adjust the combustion process based on real-time data collected, achieving optimal temperature, pressure, and other controls. For example, using fuzzy control algorithms to automatically adjust the ratio of fuel and air according to the actual situation inside the kiln, improving combustion efficiency.
(3) Establish a production data management system to record, store, and analyze various data in real-time during the production process, providing a basis for production optimization and fault diagnosis.
(3) Implementation steps
Preliminary research and scheme design
Thoroughly understand the current situation and needs of users' lime kilns, conduct a comprehensive evaluation of kiln structure, equipment configuration, process flow, etc., and develop detailed upgrade and renovation plans.
Equipment procurement, installation and commissioning
Purchase the required hardware equipment and software system according to the plan, install and debug them to ensure the normal operation of the equipment and the stability of the system.
personnel training
Train the operators of user enterprises to familiarize them with the operation and maintenance methods of the new automation control system.
Trial operation and optimization
Conduct trial runs in actual production, further optimize and adjust the system according to the operating conditions, and ensure the expected results are achieved.
Formal operation and post maintenance
After the system is officially put into operation, Jinyong Kiln provides post maintenance services, regularly inspecting and maintaining equipment and systems to ensure the long-term stable operation of the system.
3、 Benefit analysis of automation upgrade and transformation
(1) Economic benefits
Reduce energy costs
By precisely controlling the combustion process, it is expected to save more than X% of fuel consumption, greatly reducing production costs. Taking a medium-sized lime kiln as an example, it can save fuel costs annually.
Improve product quality
The stable production process and precise parameter control make the quality of lime products more stable, increase the qualified product rate, thereby enhancing the market competitiveness of the products and increasing sales revenue.
Reduce equipment maintenance costs
Due to more stable equipment operation and reduced component wear, it is expected to reduce equipment maintenance costs annually.
(2) Social benefits
conserve energy ,reduce emissions
Reducing energy consumption also lowers pollutant emissions, which has a positive impact on environmental protection and meets the national policy requirements for energy conservation and emission reduction.
Improve the automation level of the industry
Promote the development of the lime kiln industry towards intelligence and automation, and enhance the production efficiency and technological level of the entire industry.
(3) Management efficiency
Optimize production management
Automated systems can provide real-time production data, facilitating production scheduling and decision-making for enterprise management, and improving management efficiency.
Reduce labor intensity
Reduced the workload of manual operations, improved the working environment for operators, and reduced labor intensity.
The upgrading and transformation of the automation control system for lime kilns is an inevitable choice to improve the production efficiency of enterprises and achieve sustainable development. Jinyong Kiln, with its professional technical team, advanced equipment, and comprehensive service system, can provide users with high-quality automation upgrade and renovation services. Through hardware upgrades, software system development, and scientific implementation steps, we help enterprises solve the problems existing in their existing control systems, achieving a win-win situation in terms of economic, social, and management benefits. I believe that with the help of Jinyong Kiln, more lime production enterprises will achieve intelligent upgrading of lime kiln production and move towards a more efficient, environmentally friendly, and sustainable development path.