


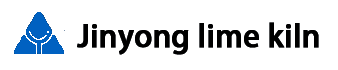
Calcination of limestone is a crucial step in lime production, involving a wide variety of equipment with unique characteristics. This article will provide a detailed introduction to commonly used equipment in the process of calcining limestone, including lime kilns, preheaters, coolers, conveying systems, etc., and analyze their respective working principles, advantages and disadvantages, and application scenarios. At the same time, the development trend of future calcination limestone equipment will also be explored, in order to provide useful reference and inspiration for lime production enterprises.
1、 Lime kiln: the core equipment for calcining limestone
Type:
Lime kiln is the core equipment for calcining limestone. According to its working principle and structural characteristics, it can be divided into two categories: vertical lime kiln and rotary lime kiln. The vertical lime kiln adopts a vertical structure, and limestone is calcined from top to bottom inside the kiln; The rotary lime kiln adopts a rotating cylinder structure, and the limestone rolls forward along the axis direction in the kiln to achieve the calcination process.
working principle:
The working principle of a vertical lime kiln is relatively simple. After limestone is added from the top of the kiln, it gradually moves downwards under the action of gravity, and is heated by the flame inside the kiln. After reaching the calcination temperature, a chemical reaction occurs to generate calcium oxide. The rotary lime kiln is even more complex. After limestone is added from the kiln head, it rolls forward in the kiln and is heated by the hot air flow, gradually reaching the calcination temperature through thermal conduction and radiation.
Advantages and disadvantages:
The advantages of a vertical lime kiln are its simple structure, convenient operation, and relatively low investment cost. However, its drawbacks are also obvious, such as low thermal efficiency, high energy consumption, and poor environmental performance. In contrast, rotary lime kilns have advantages such as high thermal efficiency, low energy consumption, and good environmental performance, but their investment and operating costs are relatively high.
Application scenario:
Vertical lime kilns are mainly suitable for small lime production enterprises or occasions with low output requirements; The rotary lime kiln is more suitable for large lime production enterprises or occasions with high output and environmental requirements.
2、 Preheater: Key Equipment for Improving Limestone Calcination Efficiency
Type:
The preheater is an important auxiliary equipment in the lime kiln system, mainly used for preheating the limestone entering the lime kiln to improve calcination efficiency and reduce energy consumption. According to its working principle and structural characteristics, preheaters can be divided into two categories: direct contact preheaters and indirect contact preheaters.
working principle:
The direct contact preheater uses the method of direct contact between hot flue gas and limestone for heat transfer. During the preheating process, limestone is heated by the hot flue gas to reach the required temperature for calcination. The indirect contact preheater uses a heat exchanger for heat transfer, and limestone exchanges heat with hot flue gas through a heat exchanger inside the preheater to achieve preheating.
advantage:
The advantage of a preheater is that it can significantly improve the calcination efficiency of limestone and reduce energy consumption. By preheating limestone, the heating time and heat consumption inside the lime kiln can be reduced, thereby reducing production costs. Meanwhile, the preheater can also improve the calcination quality of limestone and reduce the generation of unburned limestone.
Application scenario:
Preheaters are widely used in various types of lime kiln systems, whether vertical or rotary, to improve calcination efficiency and reduce energy consumption.
3、 Cooler: Key Equipment for Reducing Lime Temperature
Type:
The cooler is another important auxiliary equipment in the lime kiln system, mainly used to reduce the temperature of calcined lime for subsequent processing and storage. According to its working principle and structural characteristics, coolers can be divided into two categories: water-cooled coolers and air-cooled coolers.
working principle:
The water-cooled cooler uses water as the cooling medium to transfer the heat of lime to water through heat conduction, thereby achieving the purpose of cooling. The air-cooled cooler uses air as the cooling medium and transfers the heat of lime to the air through thermal convection, thereby achieving the purpose of cooling.
advantage:
The advantage of a cooler is that it can quickly reduce the temperature of lime, which is beneficial for subsequent processing and storage. The cooling efficiency of water-cooled coolers is high, but they require a large amount of water resources to be consumed; However, air-cooled coolers do not require water resources, but their cooling efficiency is relatively low.
Application scenario:
Coolers are widely used in various types of lime kiln systems, whether vertical or rotary, to reduce the temperature of calcined lime. When selecting the type of cooler, it is necessary to comprehensively consider the actual production needs and water resource conditions.
4、 Conveyor system: an important equipment to ensure smooth material flow
Type:
The conveying system plays a crucial role in the lime kiln system, mainly used for conveying materials such as limestone and lime. According to different conveying methods, it can be divided into various types such as belt conveyors, bucket elevators, screw conveyors, etc.
working principle:
Belt conveyors use continuous carrying belts to transport materials, bucket elevators use bucket shaped containers to lift materials from low to high, and screw conveyors use rotating spiral blades to transport materials to designated positions.
advantage:
The advantage of a conveying system is that it can achieve continuous and efficient material transportation, improving production efficiency. Meanwhile, different types of conveyors can be selected and combined according to actual production needs, with high flexibility and adaptability.
Application scenario:
The conveying system is widely used in various aspects of the lime kiln system, including the transportation of raw materials, the transportation of finished products, and the treatment of waste. When selecting a conveying system, it is necessary to comprehensively consider factors such as material properties, conveying distance, and conveying volume.
5、 Future Outlook: Development Trends of New Environmental Protection and Energy Saving Equipment
With the advancement of technology and the improvement of environmental awareness, new environmentally friendly and energy-saving equipment will become the development direction of future lime kiln systems. Specifically, future new environmentally friendly and energy-saving equipment will have the following characteristics:
Efficient and energy-saving: adopting advanced energy-saving technologies and equipment to improve energy utilization efficiency and reduce energy consumption and carbon emissions in the production process. For example, using new refractory materials and optimized combustion systems to reduce the energy consumption of lime kilns.
Low pollution: By improving process and equipment design, the emission of pollutants is reduced. For example, adopting advanced desulfurization and denitrification technologies and dust collection devices to reduce exhaust emissions.
Intelligence: Utilizing technologies such as the Internet of Things and big data to intelligently manage and control the lime kiln system, improving production efficiency and product quality. For example, implementing remote monitoring and fault warning functions.
Modularization: Adopting a modular design, it facilitates the installation, disassembly, and maintenance of equipment. For example, dividing the lime kiln system into several modules, each of which can operate and maintain independently.
Scalability: Achieve equipment expansion and upgrading based on changes in production needs. For example, increasing or reducing the number of lime kilns, adjusting the layout of production lines, etc. The development of new environmentally friendly and energy-saving equipment in the future will focus on research and application in areas such as high efficiency, energy conservation, low pollution, and intelligence, making contributions to the sustainable development of the lime industry. At the same time, lime production enterprises should actively introduce and apply these new equipment to improve production efficiency and product quality, reduce production costs and environmental risks.